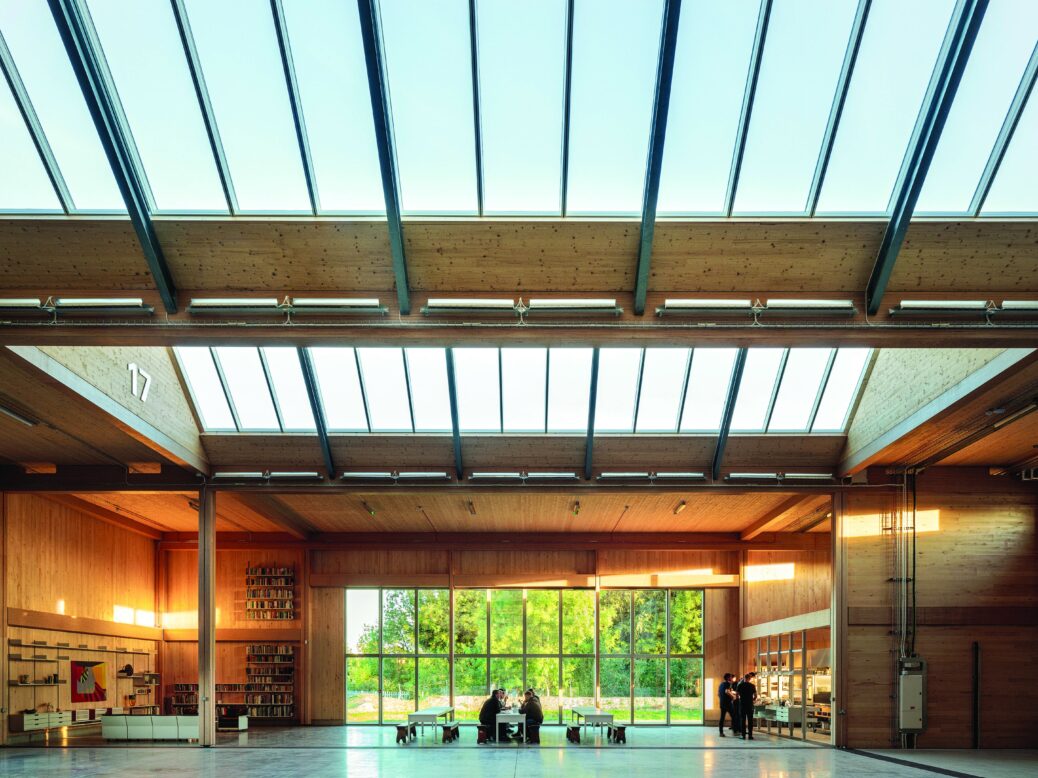
Politicians may find it hard to imagine any building that has been more influential to our history than the Palace of Westminster, but there are factories that can give Parliament a run for its money. Lombe’s Mill, built in 1721, was the first of a series of textile mills on the river Derwent that grew to employ almost everyone in the surrounding area, manufacturing products in huge volume and creating vast wealth for their owners, in a model that was eventually copied across the country and the globe. Parliament created Britain’s legal and political framework, but the factories of the Derwent Valley helped transform everything that was made and sold, laying the economic and social foundations of the modern world.
Nor did the influence of factories on the modern world end there. Jane Pavitt, head of School of Critical Studies and Creative Industries at Kingston University, recently curated SUPERSTRUCTURES: The New Architecture 1960–1990, an exhibition at the Sainsbury Centre for Visual Arts that looked at the way in which technology transformed architecture. The path to the “high-tech” buildings that define modern cities, says Pavitt, “started with a factory”.
“The definition of a factory changed in the 1960s and 70s,” says Pavitt, “and in Britain, that was part of an industrial change. Many industrial buildings were not necessarily factories of production, as in the turning of raw materials into goods, but of assembly or distribution. That may seem like a fine line, but it was important in that industrial Britain moved away from being a place of dirty, heavy industry – the smokestack, the production line, where everyone was divided by class. What interests me about high-tech buildings is the way in which they embraced the factory with a progressive model of architecture, something cleaner and organised on different lines.”
In the UK, the first of these cleaner, more progressive factories was designed in the 1960s by Richard Rogers and Norman Foster, who had met at Yale University in the US. In the States, says Pavitt, Foster and Rogers had become “interested in production techniques that allowed for quick assembly and ‘dry’ construction – buildings that could be assembled from high-tech, prefabricated components.” These were buildings that were more likely to be assembled by an engineering company than a traditional builder.
The Reliance Controls factory in Swindon was the culmination of Rogers and Foster’s early partnership. Pavitt says it represents not only a new kind of building, but a new kind of client. “It was commissioned by a new type of company – an electronics company. This industry needed clean techniques, new processes, different sorts of production spaces. Microprocessor factories are more like a laboratory and factory combined. They needed to incorporate a lot of new systems, such as cooling and cabling. That’s what interested [Rogers and Foster] – the idea of “plug-in” buildings with services routed under the floor, like the central aisle of an aeroplane.”
At a time when other factories were assembled by “construction companies, putting up sheds”, the Reliance Controls factory aimed for “the democratisation of the workforce,” says Pavitt. In its flexible interior, “workers would be in closer interaction, there would be a different interaction between worker and manager.” Whether or not the workforce inside really achieved this, she argues, “you could say that they anticipated the changes in industry that were to come. A lot of their buildings were distribution and assembly, and as industry was moving out of Britain and Europe, those were the things that
were retained.”
Today, says Pavitt, the “industrial buildings, factories, training centres, labs and research centres” of a large technology company all comprise “the industrial image – they all have a slot-together aesthetic.”
As the factories of the Industrial Revolution and the Space Age shaped both the production and the appearance of the world they inhabited, the influence of another set of technologies – the emerging fields of advanced materials, AI, automation and on-demand production – present the opportunity for a new breed of factories to reshape the world once more. Nina Rappaport, publications director at the Yale School of Architecture and author of Vertical Urban Factory, a book on the future of manufacturing, says factory architecture is diverging. While on the one hand, “you’re always going to need a giant shed to build an aeroplane”, Rappaport points out that “parts of aeroplanes can be built in smaller spaces. There’s one great example of that in New York. There’s an aeroplane parts manufacturer in an urban, multi-storey – what I call a ‘vertical urban factory’ – space, in Queens. People don’t even know it’s there.” As technologies such as 3D printing mean “it’s possible to make things anywhere”, Rappaport says a “neo-cottage industry” of smaller, distributed manufacturers is arising, “especially in cities”.
Rappaport says these manufacturers are also beginning to pool space, services and machinery in larger buildings, “in what we could call an industrial common”. In co-working manufacturing facilities such as New Lab, in New York, or Building Bloqs in London, startup companies pay by the hour to use the facilities to develop and manufacture new products. “Often they’re sustainable companies, or they’re looking at new technologies.” Rappaport says these new kinds of factory are “not just replacing someone’s garage,” but about launching new businesses. “It’s become an entrepreneurial model, a testing ground for later production. They work best when they’re not just tinkering, they’re getting a product online.”
Manufacturing has long benefited from being situated in or near cities, and Rappaport says that in many cases this is likely to continue. “Manufacturers have always wanted to be near power sources, labour sources, and entrepreneurs. I still think that’s the same.” In the future, it’s likely that manufacturing done by people will happen where people are available, and the UN forecasts that 68 per cent of the world’s population will live in cities by 2050.
Distributed urban manufacturing is also a result of wider economic change, says Rappaport. “The other thing we keep seeing is that in cities now, there are more companies, but with fewer employees. In the days of Big Industry there were company towns, and one company like Ford or GM employed everyone. Now it’s shifted to many companies.” Rappaport says this trend has increased sharply over the past decade, and that it is driven by technology. “I think there are more opportunities, with advanced manufacturing, for these small-scale companies to start up.”
A well-designed factory that works in full view can also be one of a company’s most effective marketing tools. “The factory itself becomes a spectacle,” says Rappaport. “We’re seeing combinations of retail and manufacturing as well. People love seeing stuff in process, it’s like magic.”
Another view on what the factory of the future will look like can be found in Leamington Spa, where the furniture brand Vitsoe recently opened its new factory. The factory is a huge space, 135m long, but on completion it was the most airtight commercial building in England. The whole building is made almost entirely from wood.
Mark Adams, Vitsoe UK’s managing director, says the new factory was built to reflect the company’s furniture – “a kit of parts that you can adapt, change and repair.” Built from cross-laminated timber, a building material that is increasingly popular for its efficiency and sustainability, the factory took just 23 days to put up. What Adams says is most important about it, however, is that “it is first and foremost a space for the human beings in it,” designed to give those people the positive things a building can offer – “views, natural light, fresh air… common-sense things. Wood is warm, and as humans we can feel that.”
The technology for a more human factory has existed for a long time, says Adams. The “north-lit” factories of the Victorian era, and indeed the naturally lit naves of medieval cathedrals, show how large spaces were lit in the centuries before electric lighting. “There’s no rocket science here.”
But Adams avoided using a traditional architect for the design, consulting instead with furniture designers, a yacht designer and an environmental engineer, among others. As Foster and Rogers did in designing the Reliance Controls building, “we asked how we could break away from all those divisions, which are in every crinkly-tin industrial shed you walk into,” and create “enough separation for quiet and concentration, but where, on a regular basis, problems can be solved by bumping into each other, rather than needing constantly to arrange meetings.”
This is achieved also through food; Vitsoe employees have freshly made breakfasts and lunches at long tables in front of a huge window. One visitor told Adams: “Where I come from, people go out and sit in their cars at lunch time.”
In Adams’ view, collaboration is not something that can be forced through structural design, but encouraged by pleasant surroundings, natural light, good food and a strong sense of equality among colleagues. While Adams admits that a tin shed is cheaper, he speaks passionately about the need to respect the natural world, to make products as sustainably and fairly as possible.
This, too, is a trend that will shape factories in the future. Scarcity of materials, increasing legislation for sustainability and a growing demand for ethical and sustainable products all point to a future in which production is different not just technologically but socially. The market for ethical products and services is already worth over £80bn a year in the UK, and the growth of this market comes mainly from younger consumers. For anyone who works in a factory – and who envies Vitsoe’s warm, wooden HQ – this can only be good news.